Revolutionise Your Order & Inventory Management with Workhorse
Are spreadsheets slowing you down?
Move your operation into the cloud with Workhorse, the simple, custom-built solution that fits your business perfectly.
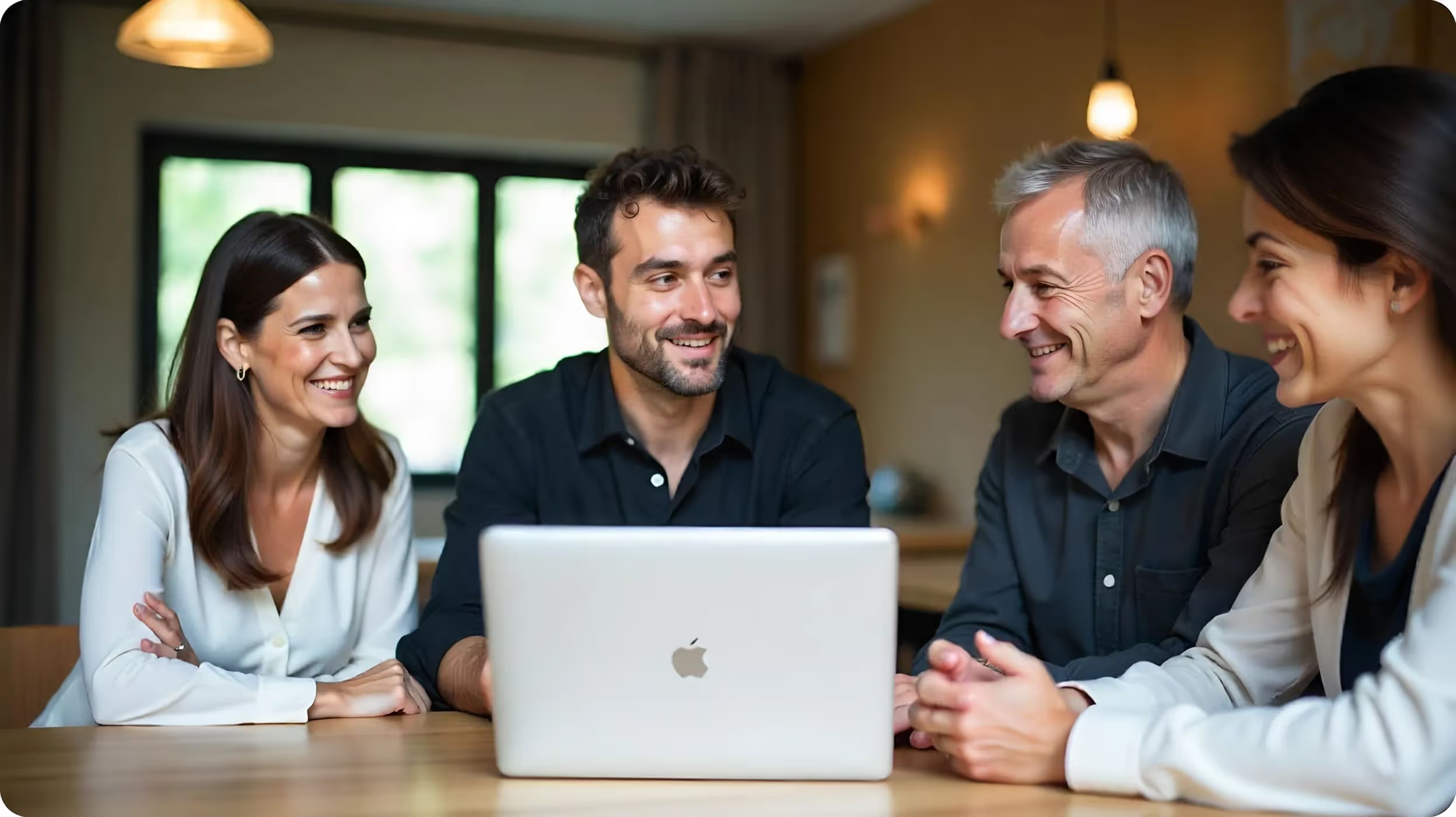
Order and Inventory Management
Stay in control of your stock and orders. Workhorse simplifies inventory tracking, reduces errors, and streamlines operations—so you can focus on growth.
Knowledge base
Get the answers you need, fast. Our knowledge base is packed with expert insights, guides, and solutions to help you make the most of Workhorse.
Powerful Features to Supercharge Your Business
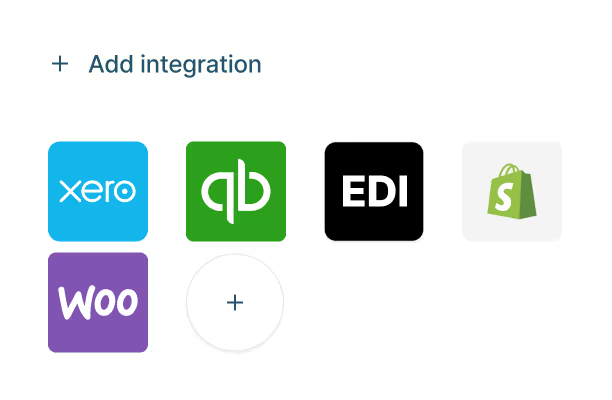
Seamless Integration
Workhorse integrates effortlessly with your existing tools and platforms and if it doesn’t already, we make it work.
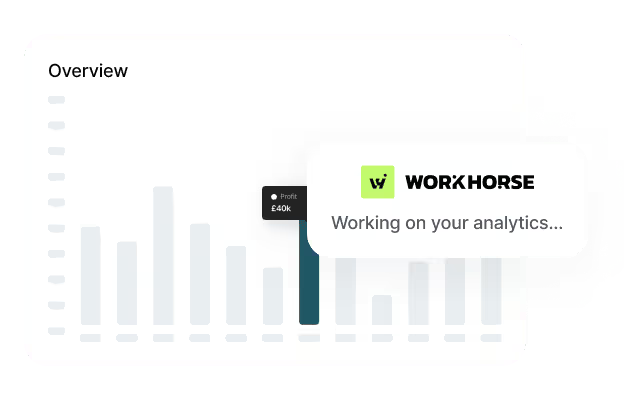
Powerful and Flexible Reporting
No more tracking data in separate spreadsheets. Workhorse's flexible application allows you to capture your data in one place, so you can easily access the reports that you need for your business.
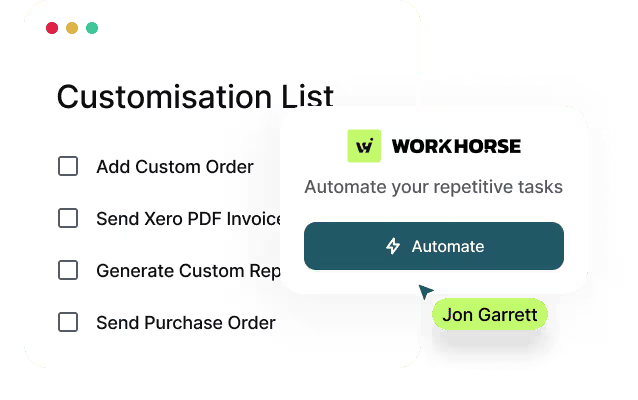
Customised Workflows
We configure Workhorse to deliver business specific workflows and automate repetitive tasks, allowing you to focus on what matters most. Ditch manual work-arounds and mundane tasks and get your time back.
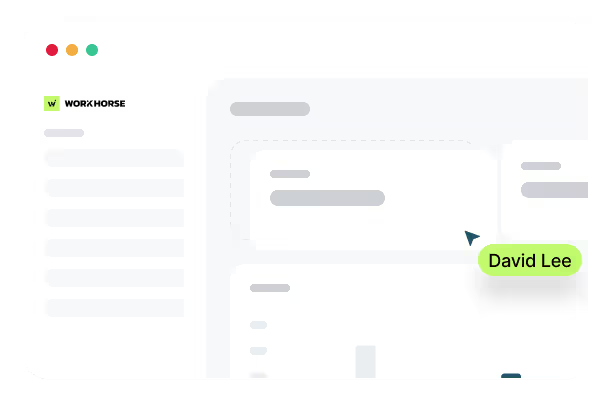
Easy To Use
Workhorse has simple, clean interface. No more complicated menus, or pages of fields you never use! Our software simplifies your operations so you can focus on what really matters.
Simple Steps to Get Started
Experience the future of CRM with seamless integration, advanced analytics, and unparalleled user experience.
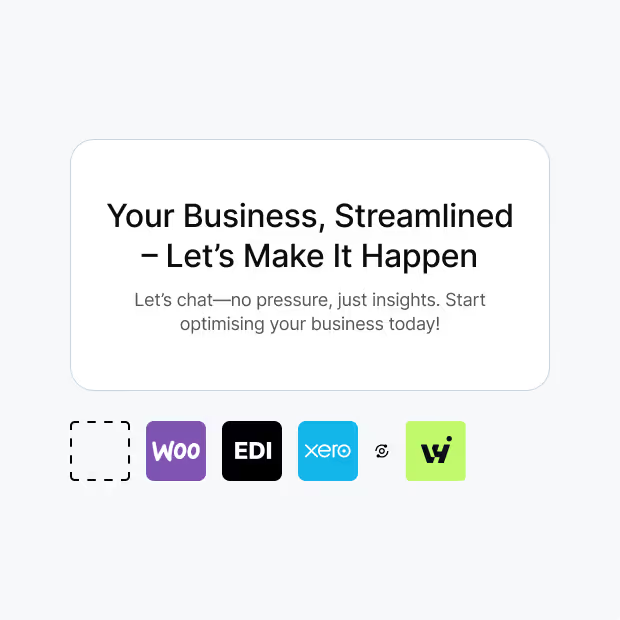
Book a discovery call
Workhorse makes it easy. We support you every step of the way by starting with a quick discovery call to fully understand your needs, so we can customise the software to fit you perfectly. Unlike every other one size fits all companies.
Schedule a call with us to go over your software needs (not a sales call!)
If it sounds like we can help we'll schedule a second call to show you our software, and discuss how it fit to your needs
We'll make sure we fully understand your needs and demonstrate how we'll solve them, before you commit to implementation.
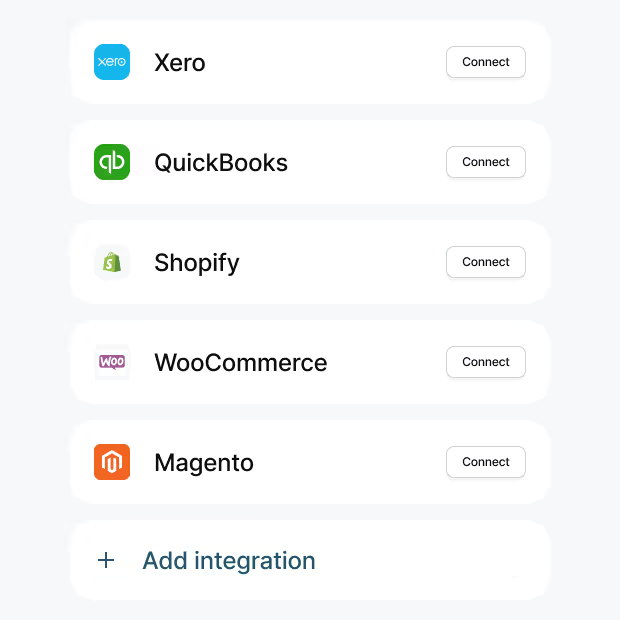
A fully supported implementation process
Your project manager will work alongside you to get you up and running with your Workhorse application, we run workshops with your team so we can fully understand your requirements. We integrate with existing tools like your website and accounting application.
Your project manager will run workshops with your team to get the ready to use Workhorse
Workhorse connects up to your website and accounting software, to ensure the seamless flow of data.
Automatically import your existing customer, supplier and product data into Workhorse for a smooth transition.
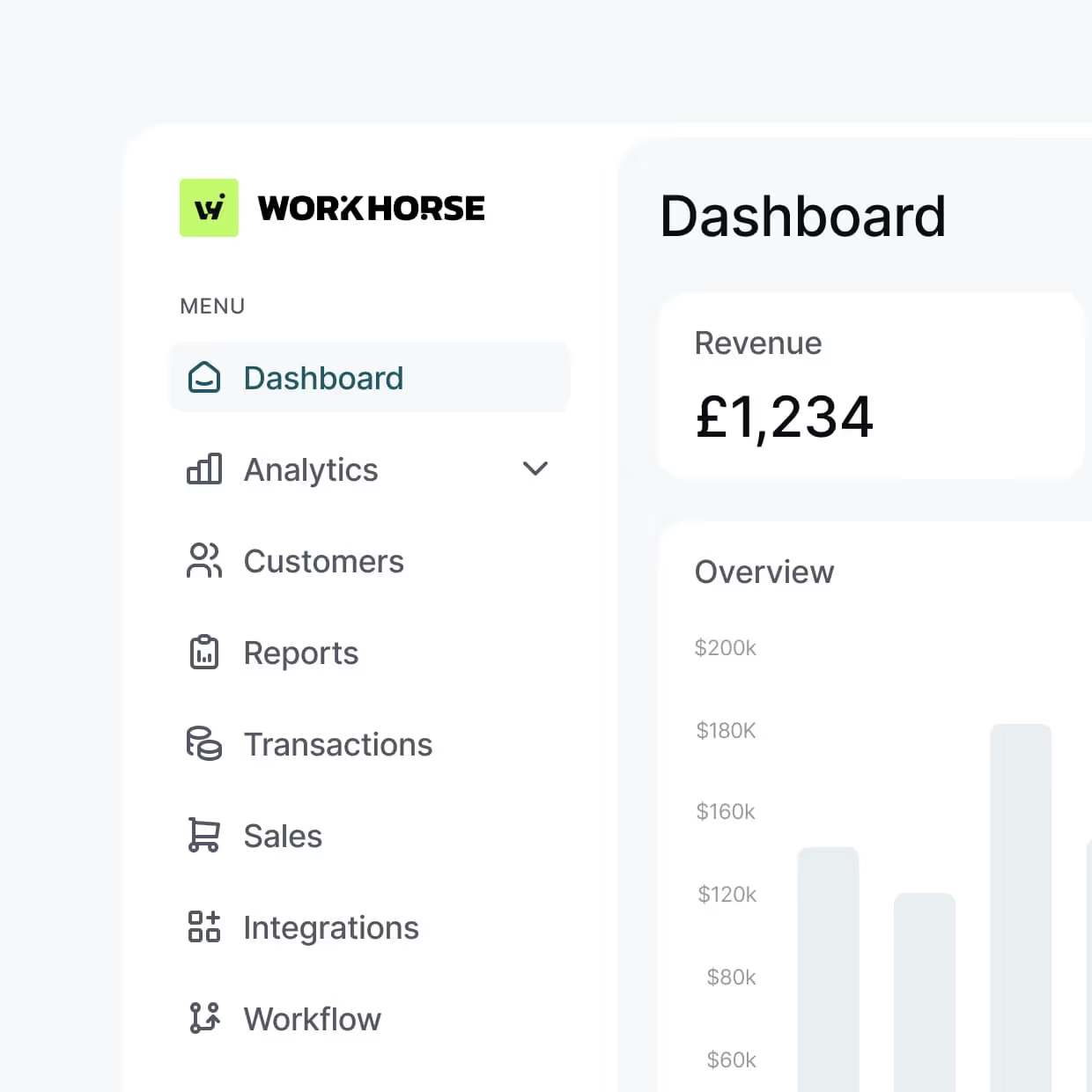
Plan for Go-Live
Our team will work alongside you to ensure you are ready for Go-Live and that you get up and running quickly and easily once you made the transition.
You'll provide us with up to date stock figures to be loaded into your application
We'll connect up your live website and accounting software to ensure data starts flowing from Day 1
Your project manager will support you in the first week's after go-live to ensure a successful transition
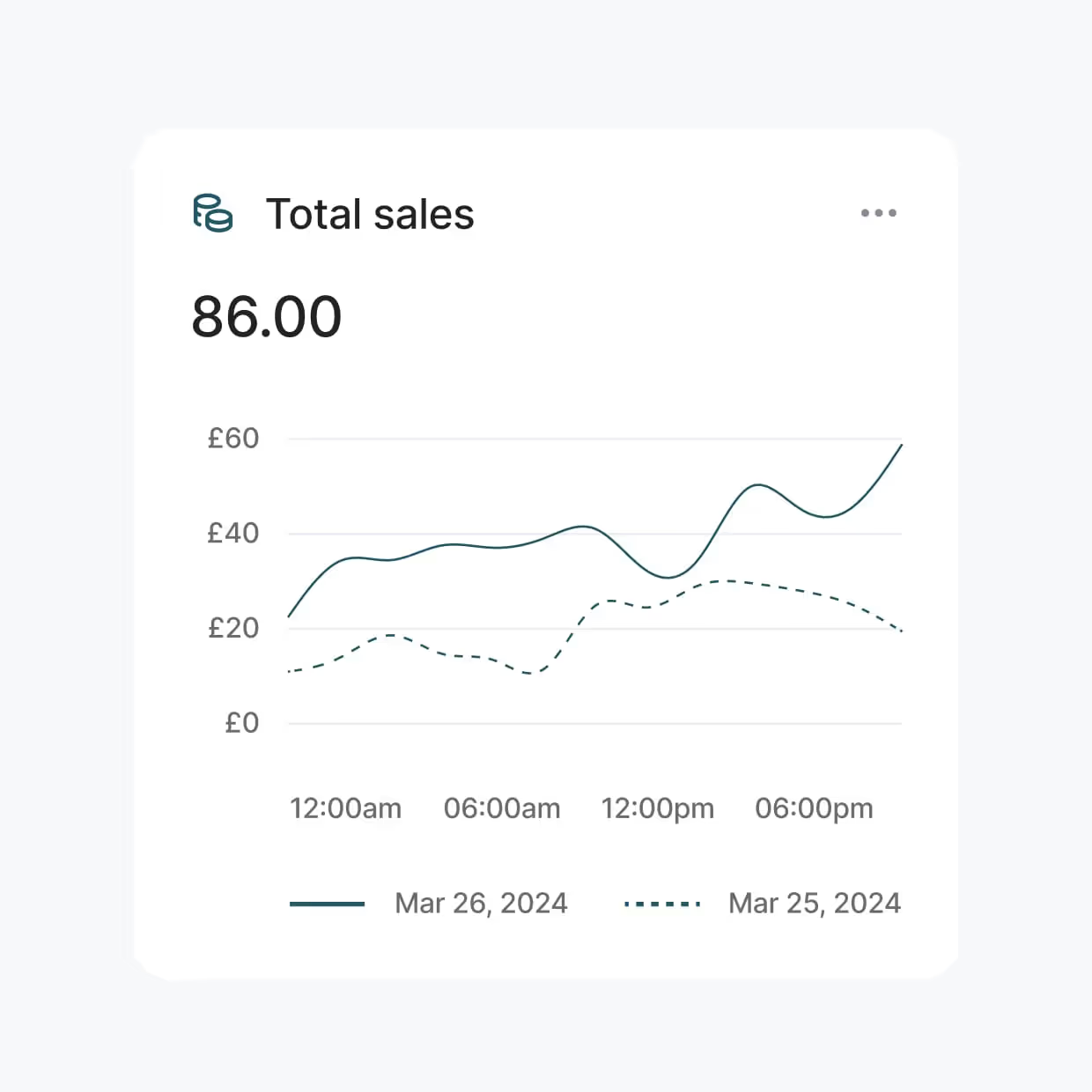
Our support team and there every step of the way
Our support analysts are there to ensure you continue to get full value from your Workhorse application as your business grows and evolves.
We offer up to 2 hours a month of functional support. Answering questions about your application and making small changes to forms, fields and reports.
Configure real-time data to stay informed about critical information.
Use Workhorse’s performance tracking tools to monitor key metrics and identify areas for improvement.
Save time and boost efficiency
Our fully customisable platform is designed around your business. Workhorse is not a ONE-SIZE fits all software, we make our software fit you.
Products and Pricing
Strip back your complex order & inventory management and keep everything in one place
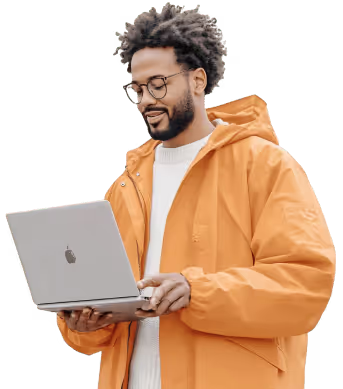
Purchasing
Strip back your complex order & inventory management and keep everything in one place
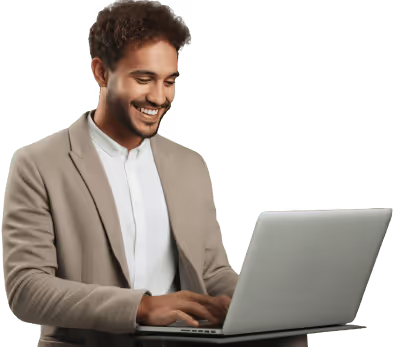
Stock Management
Gain actionable insights with analytics. All your data housed in one application.
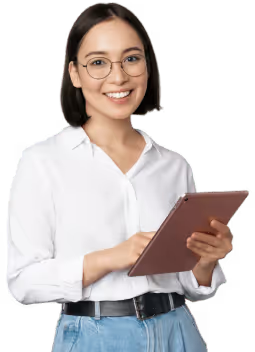
Order Fulfilment
Strip back your complex order & inventory management and keep everything in one place
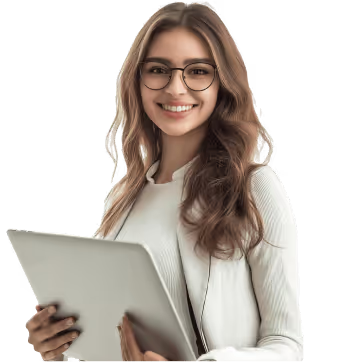
Join Hundreds of Satisfied Users
satisfaction rate
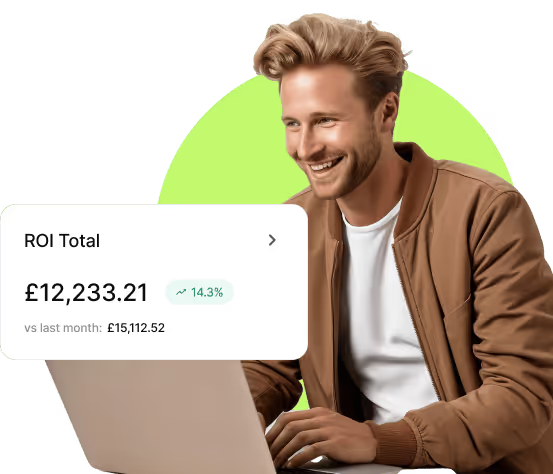
What Our Users Say
Ready to Transform Your Order & Inventory Management?
Get started today and see the difference Workhorse can make for your business.